
thesis of a ball mill method
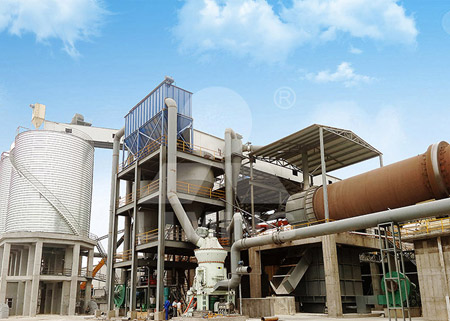
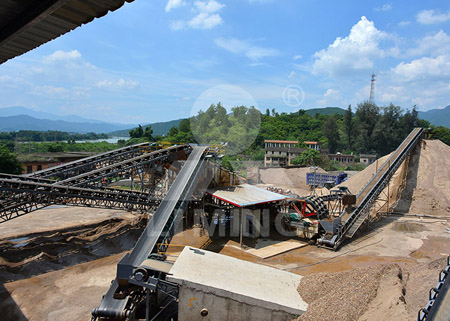
thesis of a ball mill method
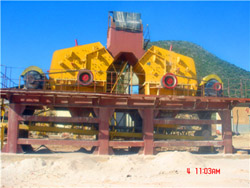
(PDF) Grinding in Ball Mills: Modeling and Process
A ball mill is a type of grinder widely utilized in the process of mechanochemical catalytic degradation. It consists of one or more The paper reviews the literature on the application of models based on distributed collision energy information to predict size (PDF) A Review of Advanced Ball Mill Modelling
احصل على السعر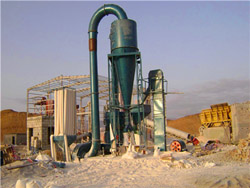
Ball milling in organic synthesis: solutions and challenges
Abstract. During the last decade numerous protocols have been published using the method of ball milling for synthesis all over the field of organic chemistry. However, compared to At present, the synthesis methods of MOFs mainly include the hydrothermal method, microwave assisted method, ultrasonic assisted method, Synthesis of Metal Organic Frameworks by Ball
احصل على السعر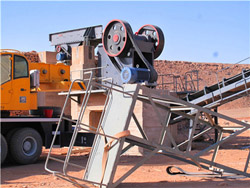
Comparative Study on Improving the Ball Mill Process
The ball mill process parameters discussed in this study are ball to powder weight ratio, ball mill working capacity and ball mill speed. As Taguchi array, also known Haley, R. A., Zellner, A. R., Krause, J. A., Guan, H. & Mack, J. Nickel catalysis in a high speed ball mill: a recyclable mechanochemical method for producing Advancing mechanochemical synthesis by combining milling
احصل على السعر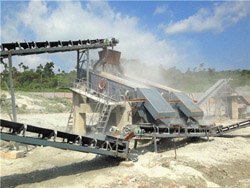
Model Study of Mechanicochemical Degradation
The process of ball milling and the materials that compose planetary ball mills are highly complex, and the existing research on the change in ball-milling energy is not mature. The theoretical model of a Abstract. Mechanochemical approaches in an organic synthesis have received increased interest because of their wide applications in green methodologies. Ball milling: an efficient and green approach for asymmetric organic
احصل على السعر
30233 PDFs Review articles in BALL MILLING ResearchGate
Explore the latest full-text research PDFs, articles, conference papers, preprints and more on BALL MILLING. Find methods information, sources, references or conduct a literature The multitude of recently reported techniques for investigating ball milling reactions, many of which are touched upon in this summary, promise to dramatically increase the pace of Methods for Monitoring Milling Reactions and
احصل على السعر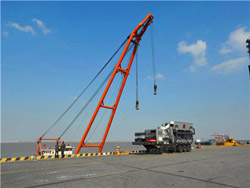
(PDF) On the Use of Ball Milling for the Production
However, the ultra-precision machining of ceramic balls, e.g., silicon nitride balls, is a difficult issue with conventional V-groove lapping technology, in which a low lapping speed (e.g., 50 rpm2.6.1 Ball size distribution in tumbling mills 37 2.6.2 Milling performance of a ball size distribution 40 2.7 Summary 41 Chapter 3 Experimental equipment and programme 43 3.1 Laboratory grinding mill configuration 43 3.2 Preparation of mono-size grinding media 44 3.3 Feed material preparation 46EFFECT OF BALL SIZE DISTRIBUTION ON MILLING
احصل على السعر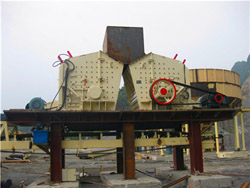
University of Liège uliege.be
In this thesis, a procedure for predicting the charge motion and the power draw of a ball mill based on the discrete element method (DEM) is calibrated and validated by means of photographs of the charge, and power draw measurements of a 1:5-scale laboratory mill, which were kindly provided by the company Magotteaux International S.A. .The ball milling method is classified as vibration mill, planetary mill and magneto-ball mill depending on the movement of the balls and vessel and among them, the planetary mill is the most common as it has been used to reduce the particle size of many materials. The ball milling process induces a reduction in the particle and crystallite sizeBall milling A green and sustainable technique for the preparation
احصل على السعر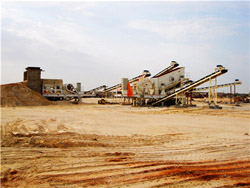
(PDF) Synthesis of Nanofertilizers by Planetary Ball Milling
For instance, high energy ball milling is a top-down method using planetary ball mills. To obtain optimized milling parameters in a planetary ball mill, many trials are needed.8.3.2.2 Ball mills. The ball mill is a tumbling mill that uses steel balls as the grinding media. The length of the cylindrical shell is usually 1–1.5 times the shell diameter (Figure 8.11 ). The feed can be dry, with less than 3% moisture to minimize ball coating, or slurry containing 20–40% water by weight.Ball Mill an overview ScienceDirect Topics
احصل على السعر
Variables affecting the fine grinding of minerals using stirred mills
It was found that the ball mill consumed 54.67 kWh/t energy to reduce the F 80 feed size of 722.2 µm to P 80 product size of 275.4 µm while stirred mill consumed 32.45 kWh/t of energy to produce the product size of 235.6 µm. It also showed that stirred mill produced finer product than the ball mill at around 40% lesser consumption of energy.the ball mass and between th e ball ma ss an d the mill liners. The si ze reduction depends mainly on the surface are as of the media in interaction (Hukki, 19 54).(PDF) Effect of ball size distribution on milling parameters
احصل على السعر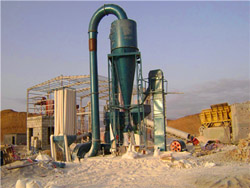
Advancing mechanochemical synthesis by combining milling
The most commonly used mills in synthetic laboratories are ball mills, Krause, J. A., Guan, H. & Mack, J. Nickel catalysis in a high speed ball mill: a recyclable mechanochemical method forAmong high-energy ball mills, the planetary is a mechanically simple and versatile device for efficient grinding. It is usually made of two or more jars, rotating at an angular velocity ω around their axis (see Fig. 1), installed on a disk rotating at angular velocity Ω.Grinding occurs by impact among the milling media (balls and jars), driven by Modeling of the planetary ball-milling process: The case
احصل على السعر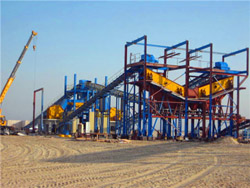
Full article: Mechanical alloying: a critical review
Mechanical alloying (MA) is a powder process that consists of repeated cold welding, fracturing, and rewelding of powder particles in a high-energy ball mill. This process is capable of synthesizing different types of non-equilibrium phases including supersaturated solid solutions, nanocrystalline materials, metallic glasses, high-entropyApplication of the discrete element method incorporating the simple kinetic model of the ball-to-ball and ball-to-wall interactions enables one to visualize the details of the grinding actions prevailing in the ball mills. The authors have developed a computer program to represent a generic mill model with which they can simulate Analysis of grinding actions of ball mills by discrete element method
احصل على السعر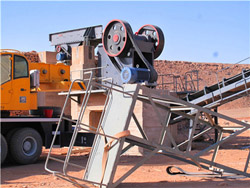
Ball milling: a green technology for the preparation and
Ball milling is a simple, fast, cost-effective green technology with enormous potential. One of the most interesting applications of this technology in the field of cellulose is the preparation and the chemical modification of cellulose nanocrystals and nanofibers. Although a number of studies have been repo Recent Review Articles Nanoscale Advances Most Popular Determining the Bond index using the Fred Bond method [1,2] is considered the state-of-the-art methodology for mill calculations and a critical process parameter in raw materials selection and grinding process control.Although it is usually referred to as a standard test, no ISO (International Organization for Standardization) or A Review of Alternative Procedures to the Bond Ball Mill
احصل على السعر
Establishing the energy efficiency of a ball mill OSTI.GOV
@article{osti_535208, title = {Establishing the energy efficiency of a ball mill}, author = {King, R P and Tavares, L M and Middlemiss, S}, abstractNote = {A method is developed to convert a measured distribution of fracture energies to the equivalent work index. The method assumes that the energy required to grind the material from the feed Taking advantage of the state-of-the-art graphene preparation technologies in China and abroad, this work studied the preparation processes of graphene for road applications based on the preliminary high-speed vibration ball milling method. This work combined numerical modeling and microscopic experiments. The preparation parameters were optimized Study on Preparation and Characterization of Graphene Based on Ball
احصل على السعر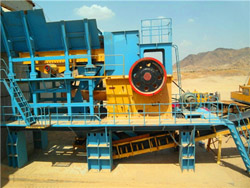
PARAMETER OPTIMIZATION OF LARGE SAG MILL LINER
The mill performance is analyzed using three parameters: useful power, percentage of useful energy consumption and tangential cumulative contact energy. In this paper, a new method for parameter design and optimization of trapezoidal liner is proposed based on DEM simulation and the Kriging model.Question. 2 answers. Sep 15, 2023. if a 5gm of copper selenide in grinded to nanoparticles by a planetary ball mill by 550rpm, 250 ml cylinder, 50 balls (10mm diameter), with ball to powder ratio245 questions with answers in BALL MILLING Science topic
احصل على السعر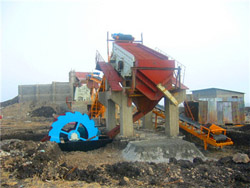
Ball Mill an overview ScienceDirect Topics
where d b.max is the maximum size of feed (mm); σ is compression strength (MPa); E is modulus of elasticity (MPa); ρb is density of material of balls (kg/m 3); D is inner diameter of the mill body (m).. Generally, a maximum allowed ball size is situated in the range from D /18 to D/24.. The degree of filling the mill with balls also influences productivity of the mill
احصل على السعر